Wealth Creation in a Precision Machined Components
Manufacturing Company
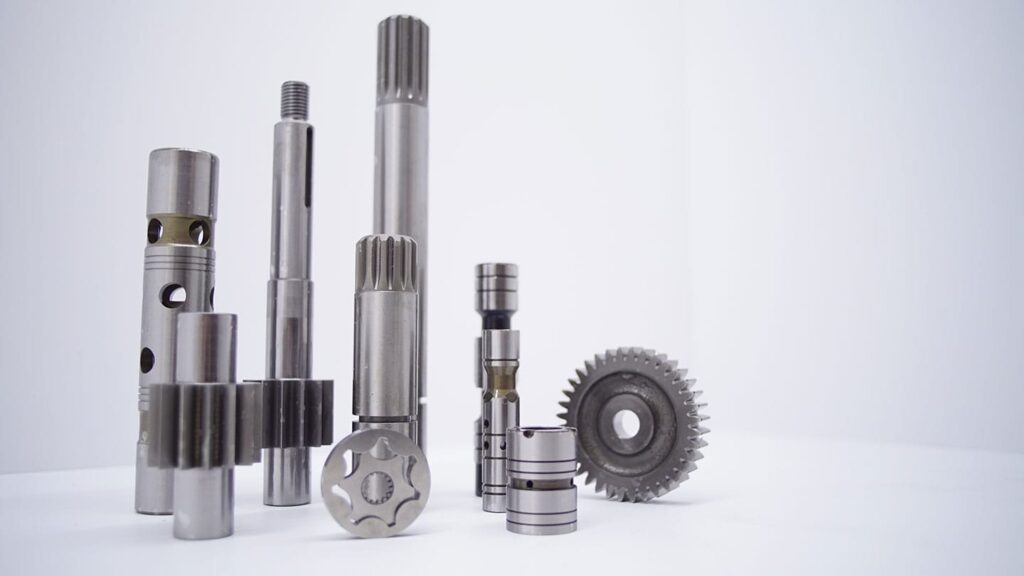
- Stagnant growth in top line
- Important & urgent need for depth in Product Mix
- Lack of clarity in the way forward
- Challenge in converting ideas, thoughts & theories into Practical/workable solutions
- Solution oriented approach to break away from recycled pools of thought which didn’t yield result
- Create a second line of structured leadership
- Maintenance related issues in key machines
- Minimum stock Raw Material not available which lead to line stoppage
- High changeover time
- Clarity on capacity requirement for a given product mix in a month’s time frame
- Identification of constraints and counter measures
- Unit wise schedule which eased the communication process
- Arrived at machine hour rate and breakeven points. Target was set based on breakeven points and tracking was started every month
- Operational P&L was prepared for machine shop and tracked on monthly basis and anchor discussed the gap along with the team
- Cycle time reduction focus was given in machine shop to increase the capacity and team had shown significant improvements in that area
- Quality standards were established and check-in points were strengthened in Incoming / In-process and final output
- Inventory control technique of A-B-C analysis was adopted in FSS store items and it brought the control on C class items
- Initiated Cost saving projects in FSS materials by involving cross functional team
- Setting revised KPIs every year & continues with the review (daily/weekly/monthly, as relevant) along with the team. It was also suggested that wherever there sustainability, is to ambiguity convert on into measurements and add in Target (KPI's) sheet
- Defining the roles and responsibilities and make people accountable. Also continuously focus on team building and engagement initiatives
- Focus on CNC / FSS marketing/order pipeline development
- Cost Optimization drive on materials, operations and quality - achieving plan vs actual schedule
The cluster approach
The cluster programme was structured in such a way that progress was reviewed by the anchor every 15 days. Tools & Techniques were explained in a classroom session, along with other cluster members. The team then had 15 days to implement the learnings on the shop floor. This was reviewed by the anchor during a plant visit and inputs were given. The team took corrective action and presented progress to the anchor & other cluster members, after the next 15 days. Inputs were taken from other cluster members as well. This cycle was continued for 12 months.
A. Background
An organization established in 1971, involved in
manufacturing of precision machined
components for aerospace, defense, mining and
industrial applications approached the institute with a need to increase top line
growth.
The manufacturing system is high varieties and low volume, customized design and
manufacturing, predominantly following “Build to customized order” and project based
manufacturing system
B. Business challenges faced
C. Approaches to the challenges
OEE Data gathering and setting up
systems to capture data
The first step was to understand the machine utilization at current level. Systems were set up to gather data and assess losses or waste in the operations so that constraints within the production process could be identified. It was done through educating the entire team starting from CEO to operator level. Since it was their first time, the initial data collected was not accurate for which continuous hand holding was done to establish accurate data collection systems.
Role clarity and assigning individual
responsibilities
Next important step was the implementation of organisation wide performance metrics (KPI’s). Organization was able to define KPIs for their business on 5 categories at the end of the cluster programme.
Targets were fixed for one year and responsibilities were defined for each member, bringing in clear accountability.
Formation of Cross Functional Team
A cross functional team was formed involving the Managing Director, the production head and the shop floor personnel in charge of the respective processes.
The team was made accountable for the achievement of the KPI and OEE targets within a specific time frame which was reviewed every fortnight by cluster anchor.
Prioritising key contributors to
business loss
After monitoring and analysing OEE data, the cross functional team, prioritised top 3 issues that were the major contributors to production cost over-run and delivery delays. They were:
Streamlining Production Planning
Process
After monitoring and analysing OEE data, the cross functional team realized that centralized planning is essential to plan, track performance of all units against target. Management had identified a key resource person for planning and control and encouraged them by giving visibility and following a review system of plan vs actual every week. The above initiative resulted in:
Application of tools and techniques:
To eliminate or reduce the identified wastes ,
the following lean tools were used - Structured
Problem Solving Techniques, 5S, Visual
Management, Root Cause Analysis, Zero Defect
techniques, Continuous improvements, SMED,
Flow Mgmt / Line Balancing.
For example, to understand the reason for not
meeting customer’s demand on time, a detailed
analysis was made for each machine centers by
taking cycle time and comparing with takt time.
This analysis helped the team to optimize
the cycle time in critical machines and to
increase the capacity
Also to address the challenge of manpower
shortages, role clarity and absenteeism, detailed
mapping was done on existing position v/s
availability, restructuring positions with job
responsibility and performance metrics. This
helped the team to overcome people related
issues like absenteeism and accountability in
the shop floor.
Periodic Review:
A system of daily meeting on fixed topics at a fixed time for 15 mins was established. Each group would meet and discuss about the critical issues and come up with solution. A DIR (Do It Right) station established for defect analysis. The challenge was to get the team oriented to observation and data collection, identifying the constraints and monitoring OEE measurement. The benefit of data gathering & monitoring was highlighted to the organisation and its employees. This improved communication among people and brought about an increase in engagement levels. Progress was reviewed on a bimonthly basis with inputs from the anchor.
Some Insights
E. Benefits Observed
Reduction in rejections by 2%
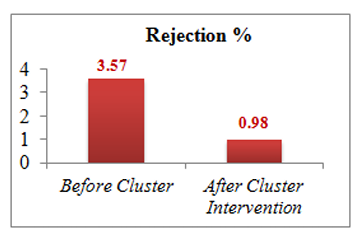
Increase in profitability by 46%
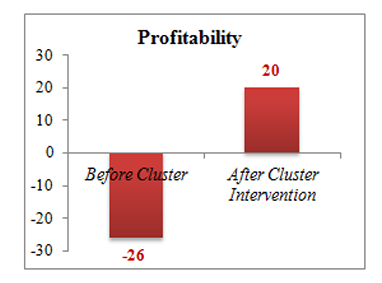
Increase in OEE from 56% to 82%
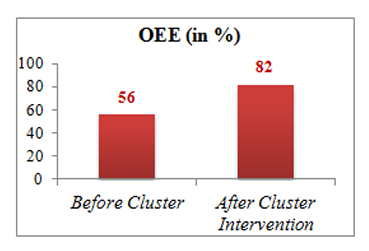
Reduction in Delivery lead time from 36 to 11 days
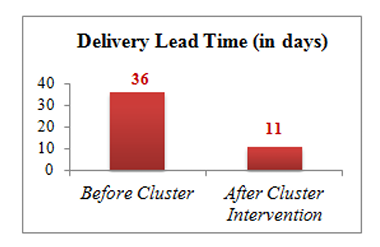
F. Conclusions and Recommendations for future growth and sustainability